QA/QC Overview
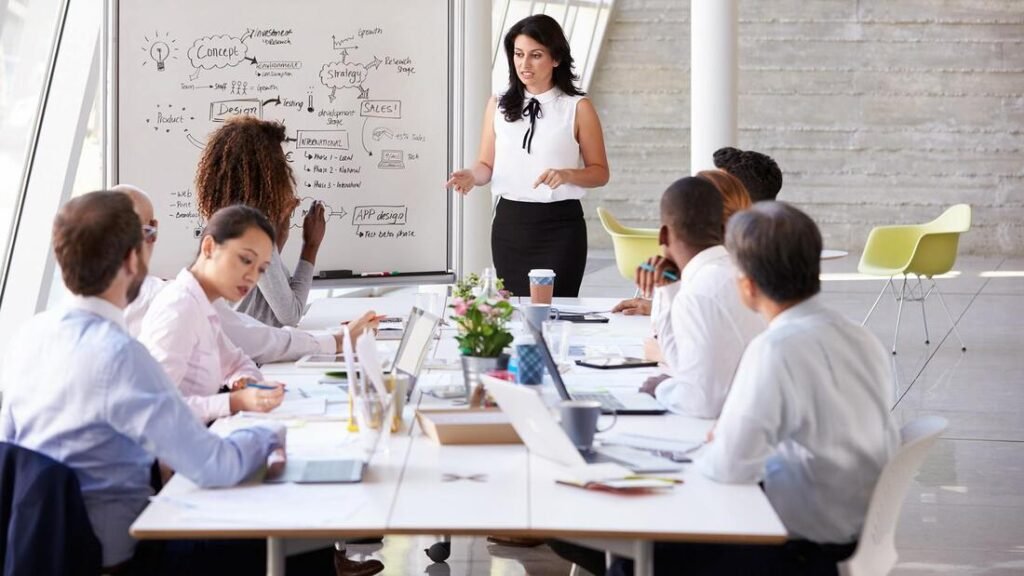
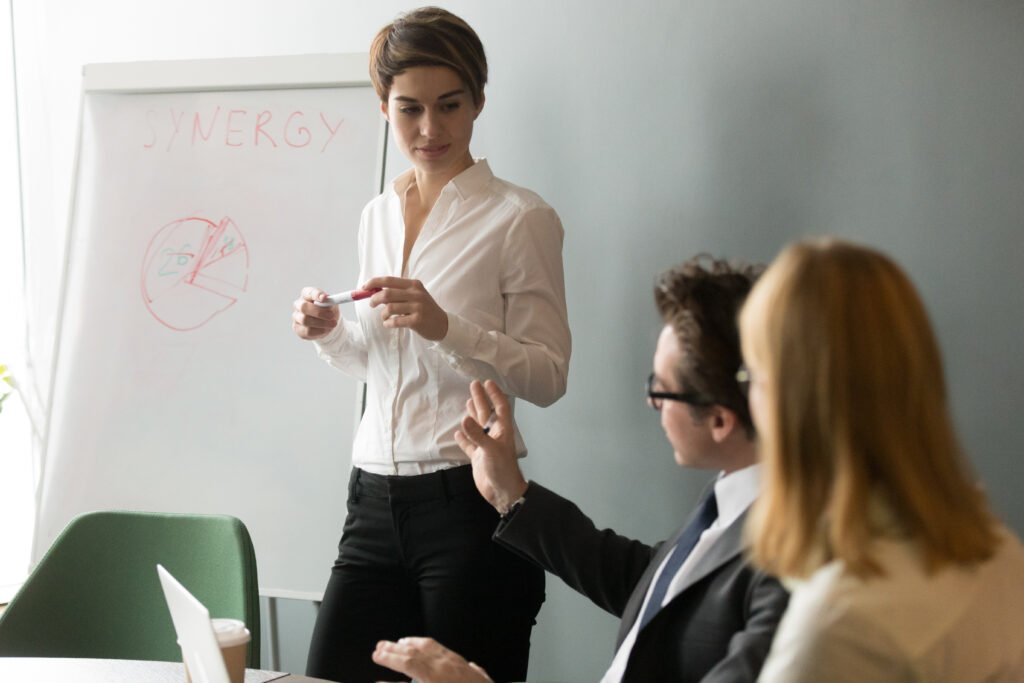
Ensuring Excellence Through Quality Assurance and Quality Control
At SICAIS Business Solutions, we recognize the importance of maintaining high-quality standards in every aspect of a business. Our QA/QC services are designed to help businesses ensure that their products, services, and processes meet regulatory and customer requirements. Quality Assurance (QA) focuses on preventing defects by improving processes, while Quality Control (QC) involves testing and inspecting products to identify and correct any issues.
Why QA/QC is Crucial for Business Success:
- Guarantees product consistency and reliability.
- Ensures compliance with industry regulations and standards.
- Enhances customer satisfaction and trust.
- Reduces waste, rework, and operational costs.
- Improves overall business efficiency and competitiveness.
Key Differences Between QA and QC
Understanding the Distinction Between QA and QC
While QA and QC are often used interchangeably, they serve different roles in maintaining quality:
- Quality Assurance (QA):
- QA is a proactive process that focuses on improving production processes to prevent defects. It involves setting up systems, procedures, and policies to ensure quality is built into every stage of production.
QA Focus Areas:
- Process improvement and standardization.
- Employee training and development.
- Continuous monitoring of production processes.
- Audits and compliance checks.
- Quality Control (QC):
- QC is a reactive process that involves inspecting and testing products after they have been produced. It identifies defects or issues that need to be corrected before the product reaches the customer.
QC Focus Areas:
- Inspection and testing of finished products.
- Identification and correction of defects.
- Statistical quality control and data analysis.
- Ensuring products meet customer and regulatory specifications.
QA/QC Processes and Tools
Key Processes and Tools in QA/QC
At SICAIS Business Solutions, we employ a range of processes and tools to ensure that businesses meet the highest quality standards:
- Standard Operating Procedures (SOPs):
- Develop and implement SOPs to ensure consistency in production and minimize human error.
- Statistical Process Control (SPC):
- Use statistical tools and techniques to monitor and control production processes, ensuring consistency and minimizing defects.
- Inspection and Testing:
- Conduct regular inspections and testing using calibrated equipment to detect and address defects at every stage of production.
- Root Cause Analysis (RCA):
- Investigate the causes of defects or process failures and implement corrective actions to prevent recurrence.
- Quality Audits:
- Perform internal and external audits to ensure compliance with industry regulations and quality standards.
Benefits of Implementing QA/QC
How QA/QC Can Transform Your Business
By implementing effective QA/QC practices, businesses can experience a wide range of benefits:
- Improved Product Quality:
- Consistently delivering high-quality products that meet or exceed customer expectations.
- Regulatory Compliance:
- Ensuring adherence to industry-specific regulations, including ISO, FDA, and other standards.
- Reduced Costs and Waste:
- Preventing defects and reducing rework or scrapping defective products, leading to lower production costs.
- Enhanced Customer Satisfaction:
- Delivering reliable products leads to improved customer satisfaction, brand loyalty, and repeat business.
- Increased Efficiency:
- Streamlining processes through continuous monitoring and improvement results in greater operational efficiency and productivity.
Why Choose SICAIS Business Solutions for QA/QC?
The SICAIS Business Solutions Advantage in QA/QC
SICAIS Business Solutions provides expert QA/QC services tailored to your specific industry needs. Here’s why you should choose us:
- Tailored Quality Solutions:
- We design and implement quality systems that align with your business objectives and industry standards.
- Experienced Quality Experts:
- Our team of seasoned QA/QC professionals brings deep industry expertise and a proven track record of success.
- Comprehensive QA/QC Support:
- From process development to final product testing, we offer end-to-end quality assurance and control services.
- Commitment to Continuous Improvement:
- We focus on long-term quality improvement, helping your business stay competitive and meet evolving customer demands.
- Compliance with Global Standards:
- Our QA/QC solutions help ensure compliance with global industry standards, including ISO, GMP, and more.